Application and development analysis of bottle cartoning machines in the pharmaceutical industry
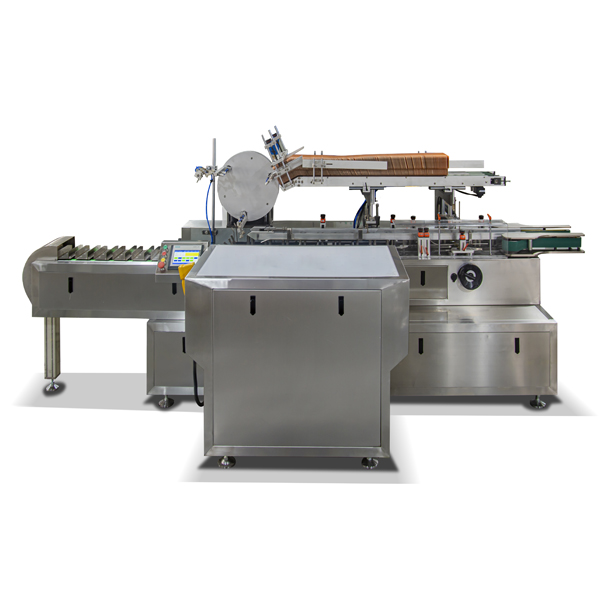
1. Application status and core functions
The bottle cartoning machine is a key equipment in the automated packaging production line of the pharmaceutical industry. It is mainly used to automatically complete the opening, filling, and sealing processes of medicine bottles (such as vials, ampoules, oral liquid bottles, etc.) and components such as instructions and labels. Its core functions include:
1. Accurate counting and positioning
Through visual recognition technology, laser scanning or sensor systems, high-precision detection of the number and position of medicine bottles is achieved to ensure the consistency of cartoning. For example, Romaco's Promatic PC4000 series uses servo drive and machine vision to adapt to the rapid switching of medicine bottles of different shapes.
2. Multi-specification compatibility
Supports a variety of packaging materials such as blister plates, hoses, and special-shaped bottles to meet the needs of different scenarios such as chemical drugs, biological drugs, and traditional Chinese medicine. Some high-end models can also integrate additional functions such as desiccant delivery and cotton ball filling.
3. Compliance and safety
Meet GMP requirements, built-in automatic cleaning (CIP) and sterilization functions to avoid cross contamination; at the same time, batch number printing and regulatory code traceability systems are used to meet the traceability of the entire drug process.
2. Technology development trends
1. Intelligent upgrade
AI and IoT integration: optimize production parameters and predict equipment failures through real-time data collection and analysis (such as Siemens PLC system supports remote monitoring).
Adaptive control system: use servo motors and modular design to reduce mechanical wear and improve long-term stability (such as Promatic PC4000's zero gear transmission technology).
2. Green manufacturing and environmentally friendly design
Lightweight materials: use degradable plastics or recycled materials to reduce transportation costs and environmental impact.
Energy-saving technology: optimize pneumatic system energy consumption, and some models have an air consumption as low as 200 Nl/min.
3. High-speed and flexible production
International leading models (such as Italy's CAMKO) have a speed of 600 boxes/minute, and domestic companies are narrowing the technology gap.
Adapt to the needs of multi-variety small batch production through fast mold change design (10-30 minutes to complete specification switching).
III. Challenges of industry development
1. Technical barriers and domestic substitution
The high-end market is still dominated by international brands such as Germany's IWKA and Italy's CAM, and domestic companies have gaps in high-speed stability and material technology.
Core patented technologies (such as visual positioning algorithms and servo drive systems) rely on imports, and the proportion of R&D investment needs to be further improved.
2. Balance between cost and efficiency
The investment cost of fully automatic production lines is high (such as Germany's IWKA equipment exceeds 1.6 million yuan), and small and medium-sized enterprises face financial pressure.
It is necessary to reduce maintenance costs through modular design and supply chain optimization (such as modular fault diagnosis to reduce downtime).
3. Regulations and market adaptability
Differences in GMP standards in various countries (such as different sterilization requirements for packaging materials in the EU and the United States) increase the difficulty of export.
Emerging markets (such as India and Brazil) have a growing demand for low-cost equipment, but they need to balance quality and price.
4. Typical cases and innovation directions
1. International benchmark cases
Krones, Germany: Launched a fully automatic high-speed cartoning line, integrating robot gripping and AI quality inspection to achieve zero manual intervention.
Romaco: The Promatic PC4000 series uses a patented box clamping system, which supports the switching of carton specifications within 30 minutes and reduces the failure rate by 40%.
2. Domestic breakthrough directions
Shanghai Pharmaceutical Packaging Machinery: Developed an intelligent cartoning machine with integrated barcode printing and anti-counterfeiting label functions, suitable for Chinese medicine granule packaging.
Counting technology innovation: Huangjiang Technology's counting machine uses a split-track vibration plate design to achieve ±1 tablet error control for tablets/capsules, in line with FDA 21 CFR Part 11 electronic record specifications.
5. Future prospects
1. Technology integration
5G and edge computing will promote real-time collaboration of equipment, and blockchain technology will enhance supply chain transparency.
2. Sustainable development
The application ratio of bio-based degradable packaging materials (such as PLA) is expected to increase to 30%, reducing plastic pollution.
3. Global layout
Chinese pharmaceutical machinery companies accelerate technology integration and expand the "Belt and Road" market through mergers and acquisitions (such as Shanghai XinGuDe's acquisition of a European technical team).
Conclusion: Bottle cartoning machines are evolving from single equipment to intelligent and integrated systems. Technology iteration and policy drive jointly promote the industry to develop in the direction of efficiency, greenness and flexibility. Enterprises need to strengthen core technology research and development, and at the same time enhance global competitiveness through international cooperation.